Noch effizienter produzieren mit höherer Qualität: Dafür sind Sensorsysteme im Einsatz. Das Sammeln von Daten ist nur ein Teil der Lösung, und auch die künstliche Intelligenz will an die Hand genommen werden.
Von Martin Stepanek
Sensoren sind aus unserem Alltag nicht wegzudenken. Temperatur- und Feuchtigkeitsfühler messen, wann Heizung, Klimaanlage oder Luftbefeuchter ihren Dienst verrichten müssen. Bewegungssensoren im Handy schlagen Alarm, wenn wir zu lange gesessen oder zu wenige Treppen gestiegen sind. Und die smarte Uhr am Handgelenk schreit auf, wenn die Herzfrequenz zu hoch wird, ein Sturz oder Unfall vermutet wird. Tausende Fehlalarme in Vergnügungsparks und Schigebieten hielten zuletzt Polizei und Rettungsdienste auf Trab.
Wie im Haushalt, wo Thermometer und andere Sensoren auch nicht erst mit den Smart-Home-Lösungen von Google, Amazon und Apple Einzug hielten, spielen Sensoren in der Industrie ebenfalls seit jeher eine Rolle, um Produktionsprozesse zu überwachen und zu optimieren. Neben Temperatur und Feuchtigkeit wird der Druck in Anlagen ebenso gemessen wie die Drehzahl von werkelnden Motoren. Aufgenommene akustische Signale sollen vor Verschleißproblemen warnen, gemessene Spannungszustände die Stabilität des Energienetzes gewährleisten.
„Sensoren sind nicht nur leistungsstärker geworden, was ihre Messfähigkeit, sondern auch ihre lokale Datenverarbeitung betrifft. Sie wurden gleichzeitig auch kostengünstiger und können daher an deutlich mehr Punkten eingesetzt werden und Informationen sammeln“, erklärt Thilo Sauter vom Zentrum für Verteilte Systeme und Sensornetzwerke der Universität für Weiterbildung Krems. Als zweiter Aspekt komme hinzu, dass die Sensordaten stärker vernetzt und kombiniert werden können und so wertvolle Rückschlüsse auf Prozesse im Bereich der Produktion, aber auch der Wartung liefern.
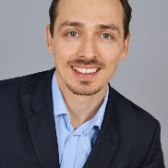
”
„Meiner Erfahrung nach setzen etwa 70 Prozent der Industriebetriebe immer noch auf eine reaktive Instandhaltung. Sie warten quasi, bis etwas ausfällt.“
Markus Loinig
Evolution statt Revolution
Das Streben nach Produktivitätssteigerungen und Kostenoptimierungen bei gleichzeitiger Qualitätssicherung ist mindestens so alt wie die Automatisierungstechnik selbst. Auch die Idee, dass Prozessinformationen transparent zusammenfließen und dann ausgewertet werden sollen, ist nicht etwas, was erst das Modeschlagwort „Industrie 4.0“ aufs Tapet brachte. Angesichts der neuen Möglichkeiten, die neben besserer Hardware auch ausgefeilte Software-Algorithmen und künstliche Intelligenz umfassen, will Sauter daher eher von einer „Evolution“ denn „Revolution“ der industriellen Produktion sprechen.
Wie wichtig Sensoren bereits in der Produktentwicklung und Prototypenphase sind, zeigt das österreichische Unternehmen AVL. Der auf Antriebs- und E-Mobilitätslösungen spezialisierte Konzern nutzt diese unter anderem, um hochpräzise Simulationen zu erstellen und diese mit Realdaten zu validieren. Im vor eineinhalb Jahren eröffneten Battery Innovation Center (BIC) wird etwa an besonders effizienten und leistungsstarken Transaktionsbatterie-Modulen und -Packs geforscht, die unter anderem mittels Laserschweißverfahren zusammengesetzt werden. „Indem wir alle Parameter der Anlage messen, können wir sicherstellen, dass der für die Prototypenherstellung aufgesetzte Prozess nicht nur reproduzierbar wird, sondern bei einer Serienproduktion die gleiche Qualität erzielt werden kann“, erklärt Martin Weinzerl von AVL.
CO2-Fußabdruck berechnet
Neben optischen Sensoren, die die Laserschweißnaht genau unter die Lupe nehmen, sind Temperatur- und Feuchtigkeitssensoren für den Klebeprozess und Kraftsensoren für die Qualitätsabsicherung wichtig. Über die Sensoren kann laut Weinzerl auch für jeden Prozess gemessen werden, wie viel Energie und CO2-Äquivalente aufgewendet wurden. Den CO₂-Fußabdruck in der Batterieproduktion schon in der Prototypenphase für eine etwaige Serienproduktion berechnen zu können, sei angesichts des geplanten EU-weiten Batteriepasses und des Bemühens um mehr Nachhaltigkeit in der E-Mobilität unerlässlich.
Neben der Optimierung von Produktionsprozessen noch vor der Serienreife, spielen Sensoren in der Zustandsüberwachung von bestehenden Fertigungsabläufen, aber auch in der Vorhersage eine gewichtige Rolle. Denn wo in der Produktion oder im Betrieb mechanische Teile im Einsatz sind, ist der Verschleiß und der Ausfall von Komponenten nur eine Frage der Zeit.
Verschleiß erlauschen
Verschleißteile in praktisch jeder Anlage - von Generatoren, Turbinen und Pumpen über diverse Arten von Motoren und Förderbändern bis hin zu Papierwalzen - sind die Wälzlager. Lange bevor die Lager kaputt werden, lassen sich Beeinträchtigungen über akustische Veränderungen erkennen. Entsprechend angebrachte Sensoren können folglich Hinweise darauf geben, ob und wann die jeweilige Komponente getauscht werden muss.
Die österreichische Firma Senzoro hat diesbezüglich einen innovativen Weg gewählt. Bei der Vorhersage, wie lange ein Wälzlager noch funktionstüchtig ist, vertraut sie auf mobil einsetzbare Sensoren und künstliche Intelligenz (KI). „Nach dem Sammeln von zig Datensätzen über mehrere Jahre hat die KI ab einem gewissen Punkt gelernt, Beschädigungen von Wälzlagergetrieben generisch zu erkennen und die wahrscheinliche Restlebensdauer zu errechnen“, erklärt Firmengründer Markus Loinig.
Da die Sensoren nicht verbaut, sondern temporär magnetisch auf dem Gehäuse der Lager befestigt werden, seien die Kosten auch für kleinere und mittlere Betriebe stemmbar. Darüber hinaus komme das System ohne langwierige Projekt- oder Lernphase aus, sei also sofort einsatzbereit. „Meiner Erfahrung nach setzen etwa 70 Prozent der Industriebetriebe immer noch auf eine reaktive Instandhaltung. Sie warten quasi, bis etwas ausfällt, und müssen dann sehr schnell reagieren oder improvisieren“, sagt Loinig. Angesichts hoher Kosten für Ersatzteile und der unterbrochenen Produktion sei das zwar verständlich. Eine vorausschauende Planung helfe aber, die Wartung und alle damit verbundenen Unannehmlichkeiten in Ruhe und gezielt zu koordinieren.
Massenhaft Daten
Dass am Einsatz künstlicher Intelligenz in der Industrie kein Weg vorbeiführt, liegt auch für Matthias Kahr vom Zentrum für Mikro- und Nanosensorik an der Universität für Weiterbildung Krems auf der Hand: „Wir haben mittlerweile die notwendige Sensorik und massig Daten, aber kommen mit der Interpretation und Analyse kaum nach.“ Abgesehen von der bereits skizzierten Vorhersage, wann ein Schaden auftrete, werde man künftig auch besser verstehen, warum dieser auftrete.
Wie auch Sauter geht Kahr davon aus, dass die Datenverarbeitung und Intelligenz noch stärker zu den Sensorsystemen selbst wandern, die künftig zu leistungsfähigen Minicomputern werden. Indem nicht alle gesammelten Daten an einen zentralen Server und wieder zurück gesendet werden müssen, kann man so dem seit jeher bestehenden Problem begrenzter Leitungskapazitäten entgegenwirken. Diese seien - nicht zuletzt durch 4G- und 5G-Technologien - gestiegen, gleichzeitig habe die Datenmenge aber derart zugenommen, dass das Problem weiterhin evident sei, betont Sauter.
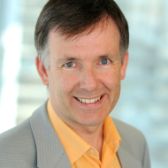
”
„Um industrielle Prozesse mithilfe von KI optimieren zu können, muss man schon wissen, wonach man sucht.“
Thilo Sauter
KI braucht Vorsortierung
Damit das Potenzial von maschinellem Lernen ausgeschöpft werden kann, ist es nach Ansicht der Fachleute jedenfalls unerlässlich, dass man über Prozess-Know-how verfügt und die künstliche Intelligenz entsprechend mit vorsortierten Daten füttert. „Das ursprüngliche Versprechen von Big Data, einfach alles zu sammeln und die KI löst dann alle Probleme, hat sich gerade in der Industrie nicht erfüllt. Um industrielle Prozesse mithilfe von KI optimieren zu können, muss man schon wissen, wonach man sucht“, sagt Sauter.
Das bestätigt auch AVL-Projektmanager Martin Weinzerl, dem als Vision einer Industrie 5.0 eine Schwarm-Intelligenz vorschwebt. So könnten KI-Systeme, die auf Anlagen auf der ganzen Welt verteilt sind, ihre Lernerfahrungen künftig verschlüsselt miteinander teilen. Ein übergeordnetes System könnte aus den übermittelten KI-Erfahrungen eigene Schlüsse ziehen und so die Prozessoptimierung auf ein völlig neues Level heben. Bis dahin ist es allerdings noch ein gutes Stück Weg.
Martin Stepanek ist Wissenschaftsjournalist bei der Tageszeitung "Der Standard"
THILO SAUTER
Priv.-Doz. DI Dr. Thilo Sauter ist Senior Scientist am Zentrum für Verteilte Systeme und Sensornetzwerke des Departments für Integrierte Sensorsysteme. Er forscht zu smarten Sensoren und Netzwerken in der Automation mit Fokus auf Echtzeit-, Sicherheits- und Integrationsaspekten.
MARTIN WEINZERL
DI Martin Weinzerl studierte an der TU Graz Wirtschaftsingenieurswesen-Maschinenbau mit dem Schwerpunkt Mechatronik. Der Senior Project Manager bei AVL koordiniert nationale sowie europäische Forschungsprojekte.
MARKUS LOINIG
DI Mag. Markus Loinig gründete nach seiner Tätigkeit im Bereich Lean Management bei der Daimler AG und in der Unternehmensberatung Booz & Company sein eigenes Unternehmen Senzoro, das im Bereich Industriesensoren Ultraschalltechnologie mit künstlicher Intelligenz kombiniert.
MATTHIAS KAHR
DI Matthias Kahr, BSc ist wissenschaftlicher Projektmitarbeiter am Department für Integrierte Sensorsysteme der Universität für Weiterbildung Krems, wo er am Zentrum für Mikro- und Nanosensorik forscht.
Artikel dieser Ausgabe
Tags